How to manufacture sieve plates
Manufacturing sieve plates involves several steps. Here is a general overview of the process:
Material Selection: Choose a suitable material for the sieve plate based on the application requirements, such as the desired strength, corrosion resistance, and compatibility with the material being sieved. Common materials include stainless steel, carbon steel, or other alloys.
Sheet Metal Preparation: Obtain sheet metal of the chosen material in the required thickness. Ensure the sheet is clean and free from any contaminants or surface defects.
Design and Layout: Determine the dimensions, hole size, pattern, and spacing of the sieve plate based on the specific sieving requirements. This design can be created using computer-aided design (CAD) software or manually.
Marking and Cutting: Transfer the design onto the sheet metal by marking the locations and outlines of the sieve plate holes. Use appropriate measuring tools and templates for accuracy. Cut the sheet metal along the marked lines using methods like shearing, laser cutting, or plasma cutting.
Hole Punching or Drilling: Create the holes in the sheet metal according to the specified pattern. This can be done using specialized hole punching machines that are set up with the required hole diameter and spacing. Alternatively, drilling machines equipped with suitable drill bits can be used for hole creation.
Deburring and Smoothing: After hole punching or drilling, remove any burrs or sharp edges around the holes. This can be achieved through deburring techniques, such as filing, grinding, or using deburring tools. Smooth the surface of the sieve plate to ensure it is even and free from rough spots.
Shaping and Forming: If necessary, shape the sieve plate into the desired form or curvature using bending or forming processes. This step may involve the use of press brakes, rollers, or other forming equipment to achieve the desired shape.
Surface Treatment: Apply any required surface treatments to enhance the sieve plate's properties. This may involve processes such as passivation, electroplating, or coating to improve corrosion resistance or promote specific characteristics.
Quality Assurance: Inspect the manufactured sieve plates for dimensional accuracy, hole alignment, and overall quality. Conduct visual inspections, measurements, and any necessary testing to ensure they meet the specified standards.
Packaging and Delivery: Package the sieve plates appropriately to protect them during transportation. Use suitable packaging materials to prevent damage or deformation. Ship the manufactured sieve plates to the designated location.
It is important to note that the manufacturing process for sieve plates can vary depending on the specific requirements, complexity of the design, and available equipment. Consulting with experienced manufacturers or engineers in the field can provide more detailed guidance and expertise tailored to your specific needs.
sieve plates
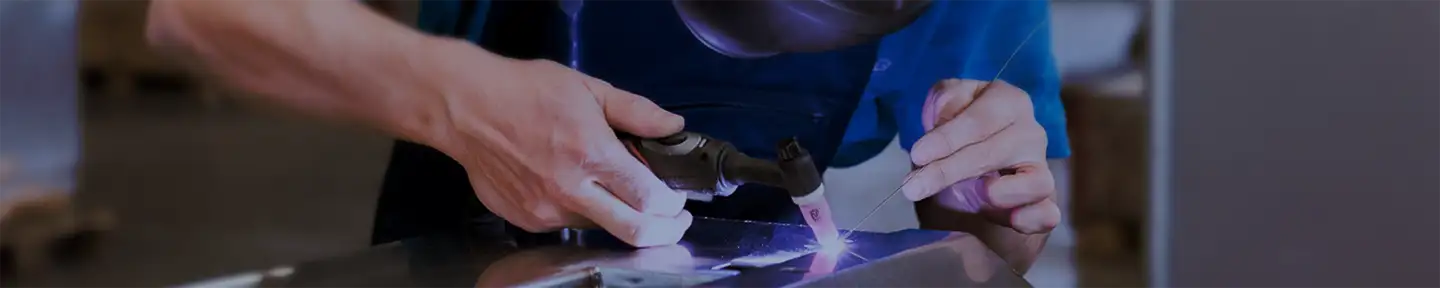
The Indian government is considering revising the steel export tariff policy
Live chat